Annals of Forensic Carpentry, Vol. 2, No. 1
Posted on 18 September 2012
Winston, my co-worker, arrived at the job site a few minutes before me, and called because he thought he was in the wrong place. “I thought we were looking at a rotten porch. The place I’m looking at is new construction.”
The triple-decker condo building in Jamaica Plain was completed in late 2005, but one of the owners called me recently to look at problems with the rear decks.
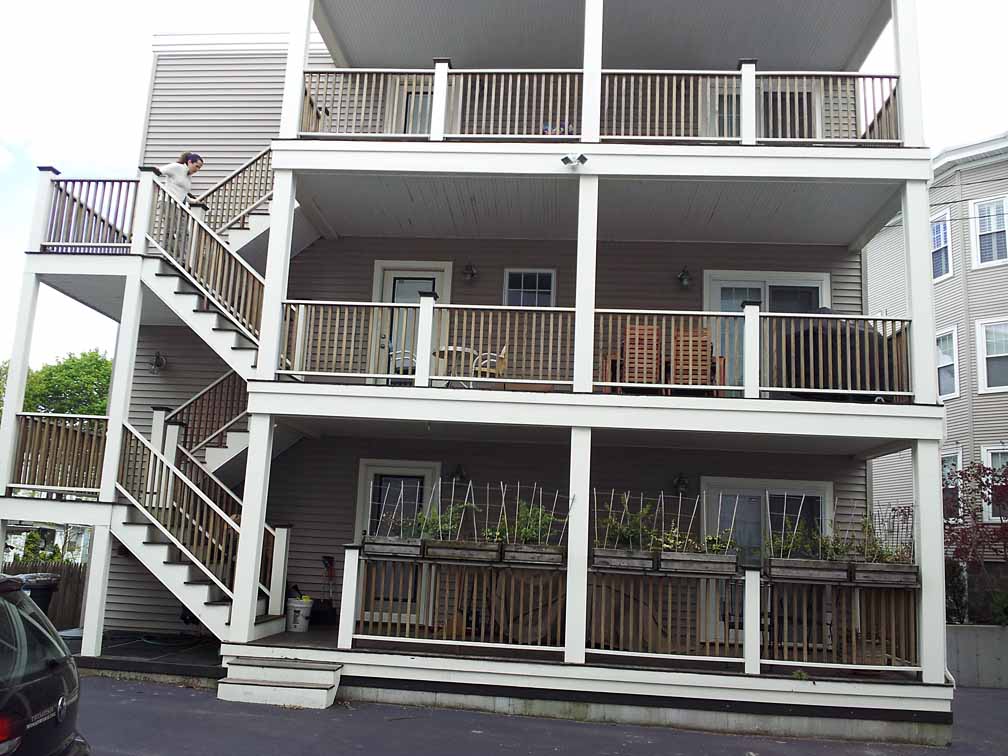
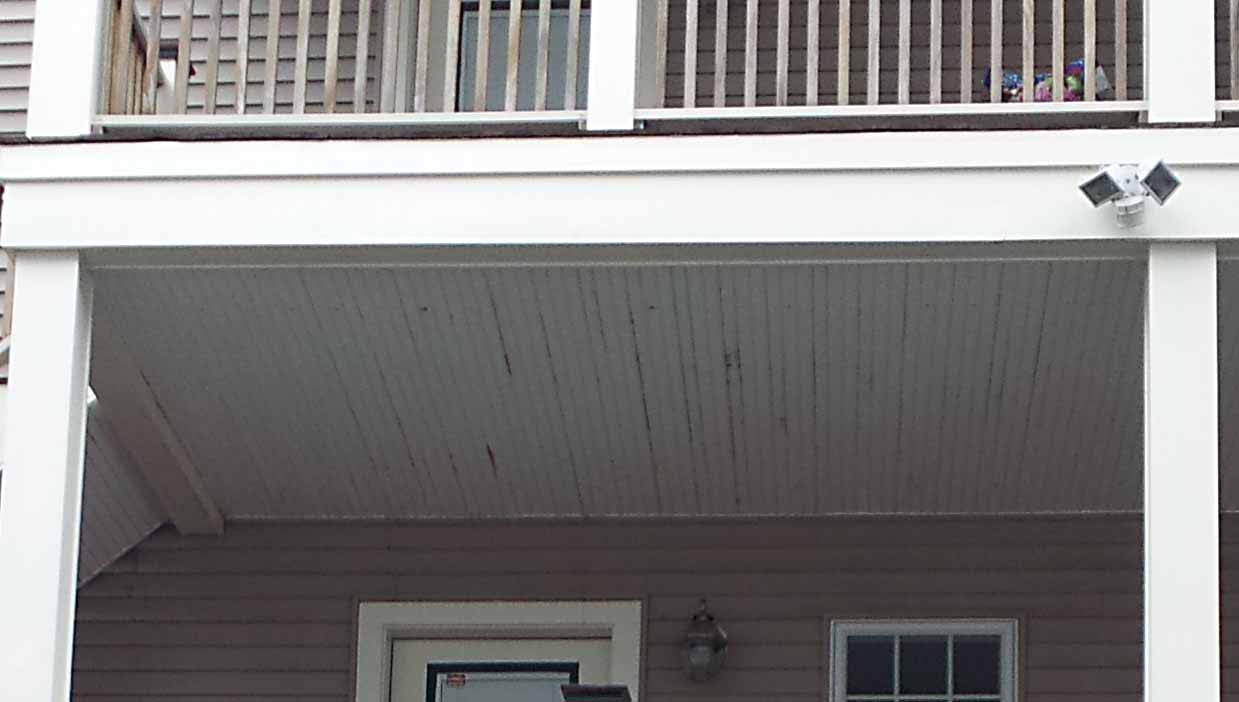
The first sign of problems was the brown staining on the white ceiling — visible if you look closely at the second floor ceiling above. Then the client showed me some of the failing deck boards.
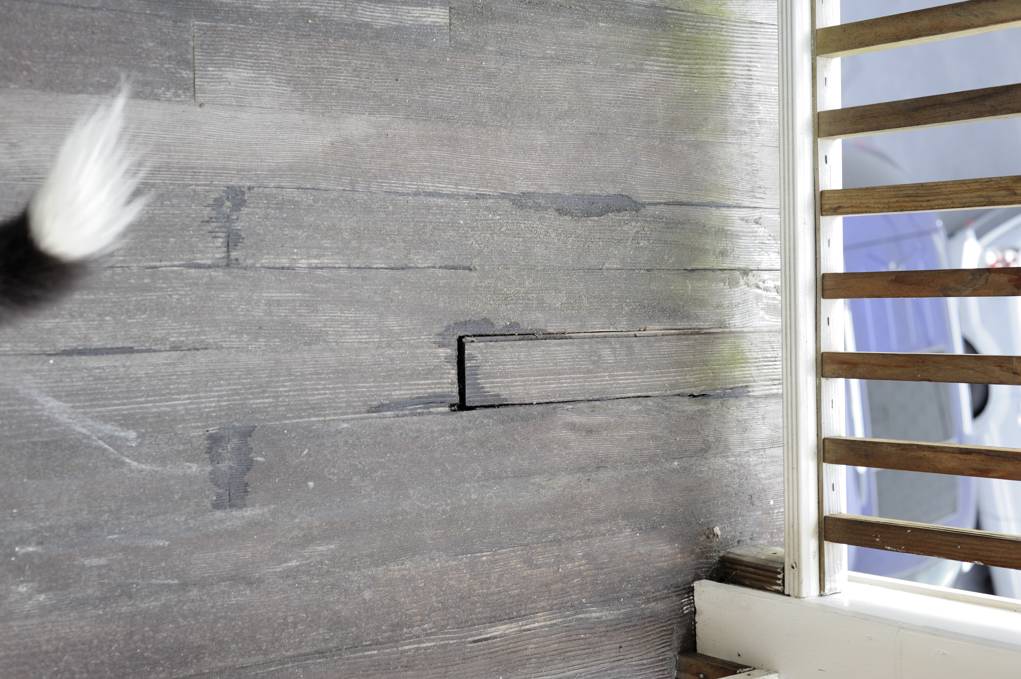
and up close:
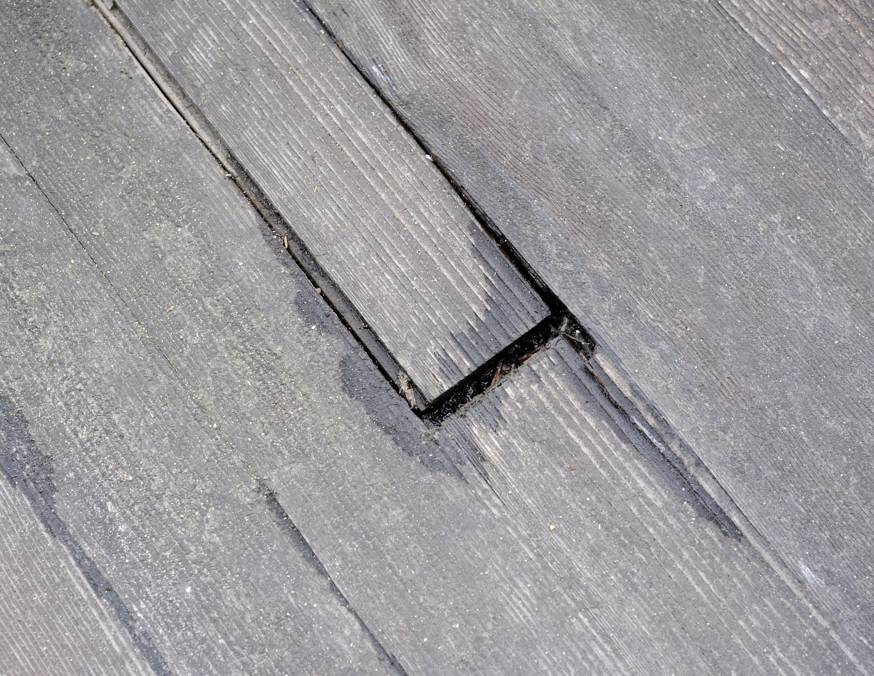
In one location, they had replaced some of the decking, but the replacements were now failing as well (with Musti for scale):
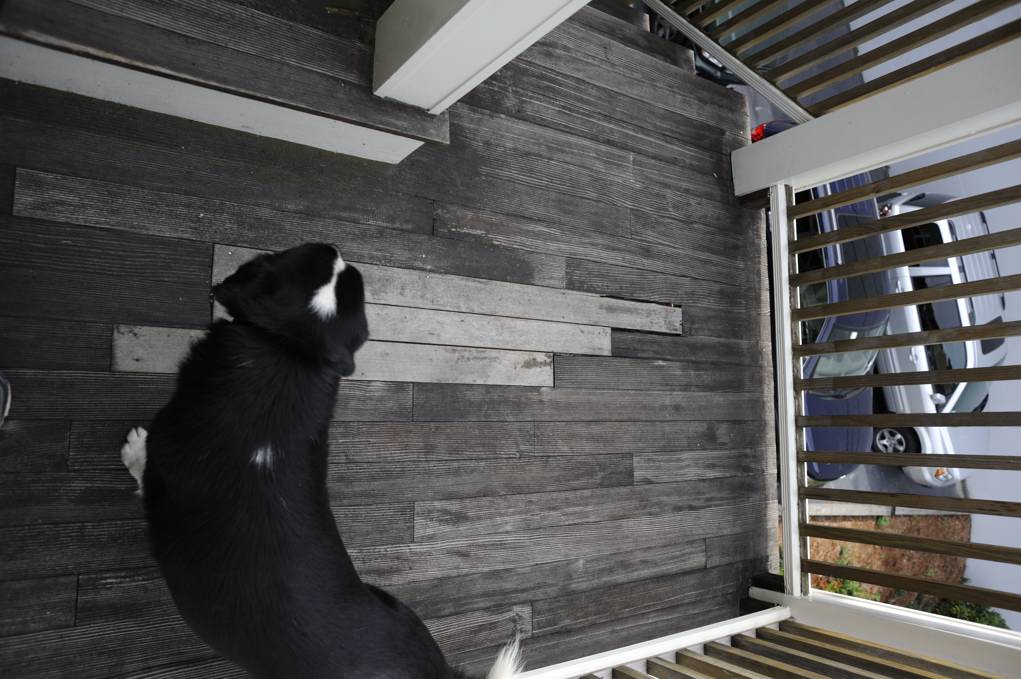
Soon the cause, if not the extent, of the problem started to be clear. The builders had framed the decks without any pitch to promote drainage. Furthermore, they had installed tongue-in-groove fir decking over plywood (see photos below) on the deck surface and plastic imitation-beadboard ceilings underneath. All of these details combined to create a chronically wet state inside the floor system: Water falling on the deck tended to stay in place, saturating the fir and plywood, and anything that dripped through got trapped by the plastic below. Not so good.
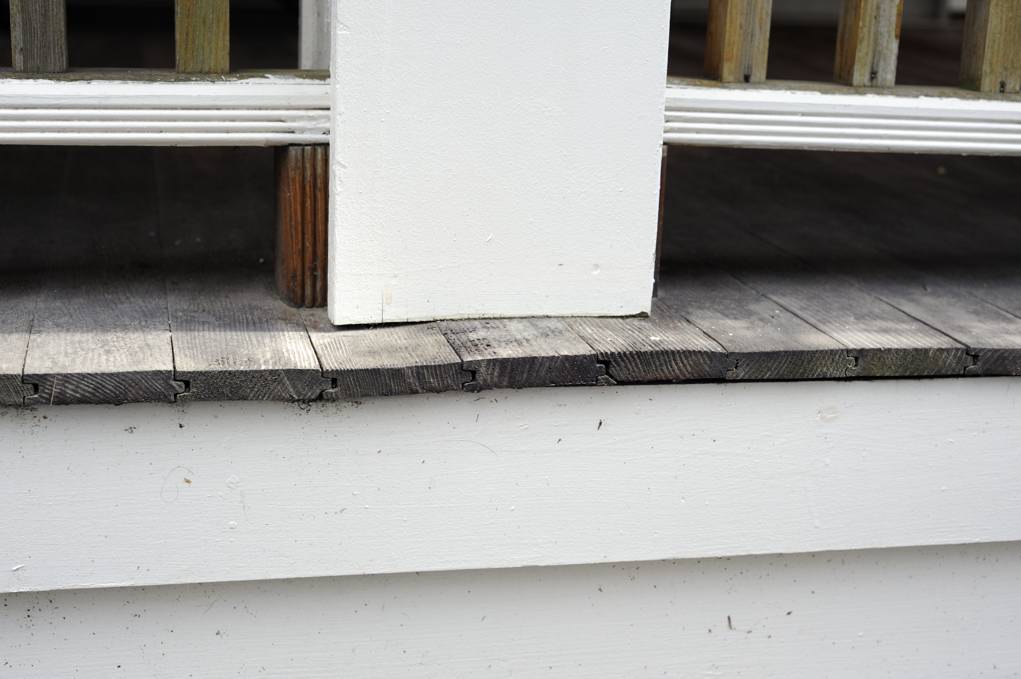
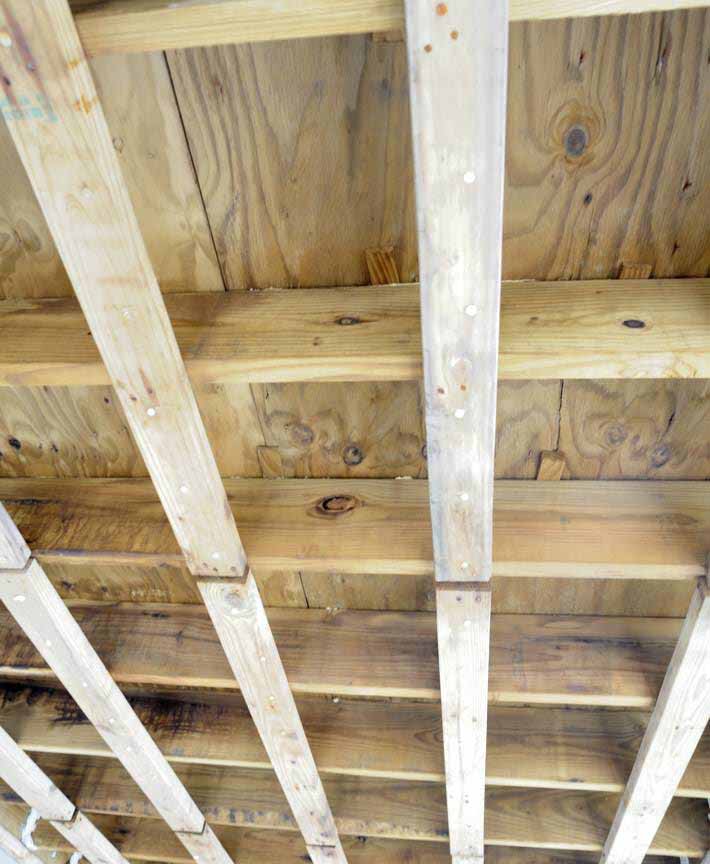
What we should have seen is something like the following:
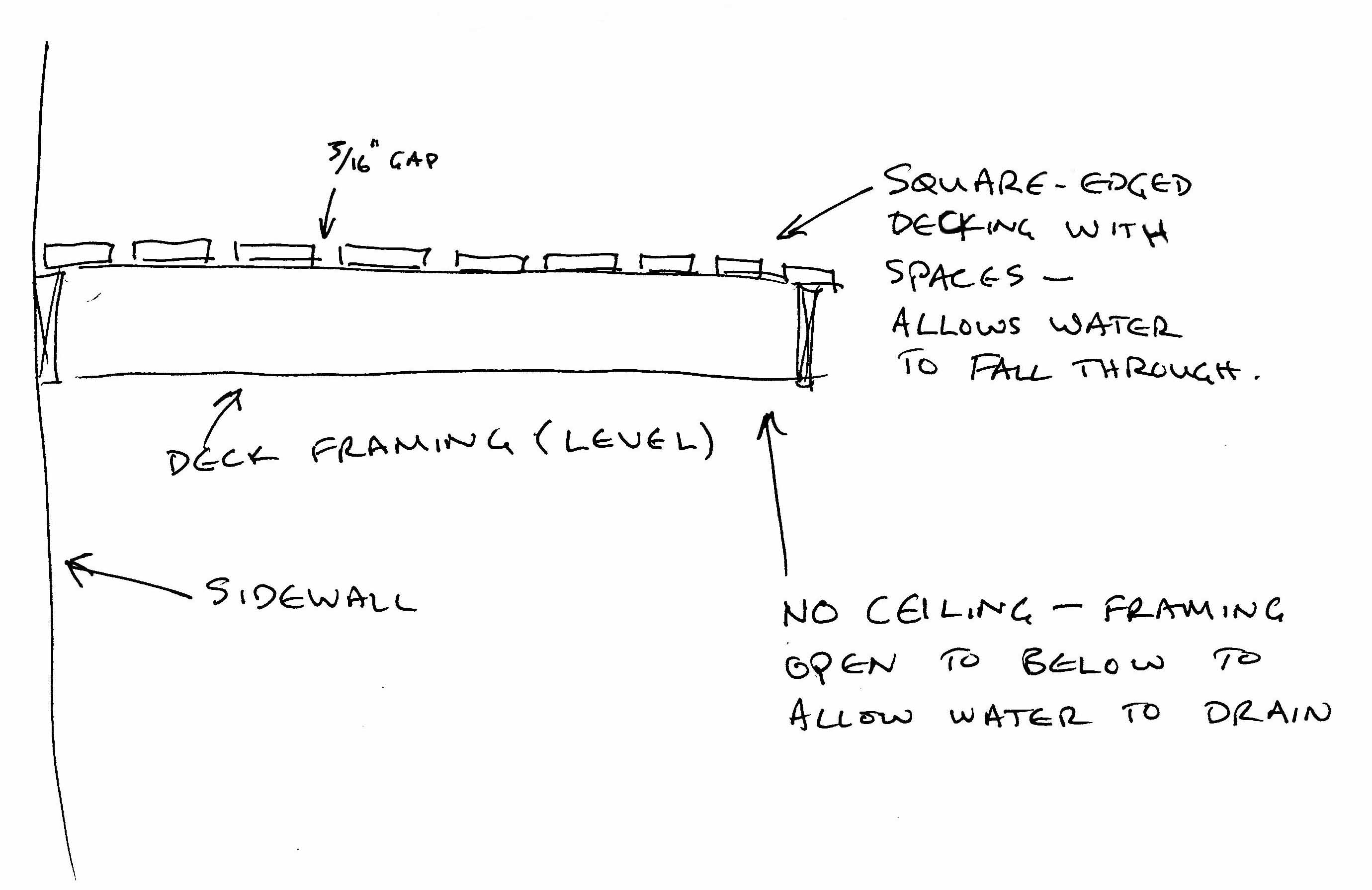
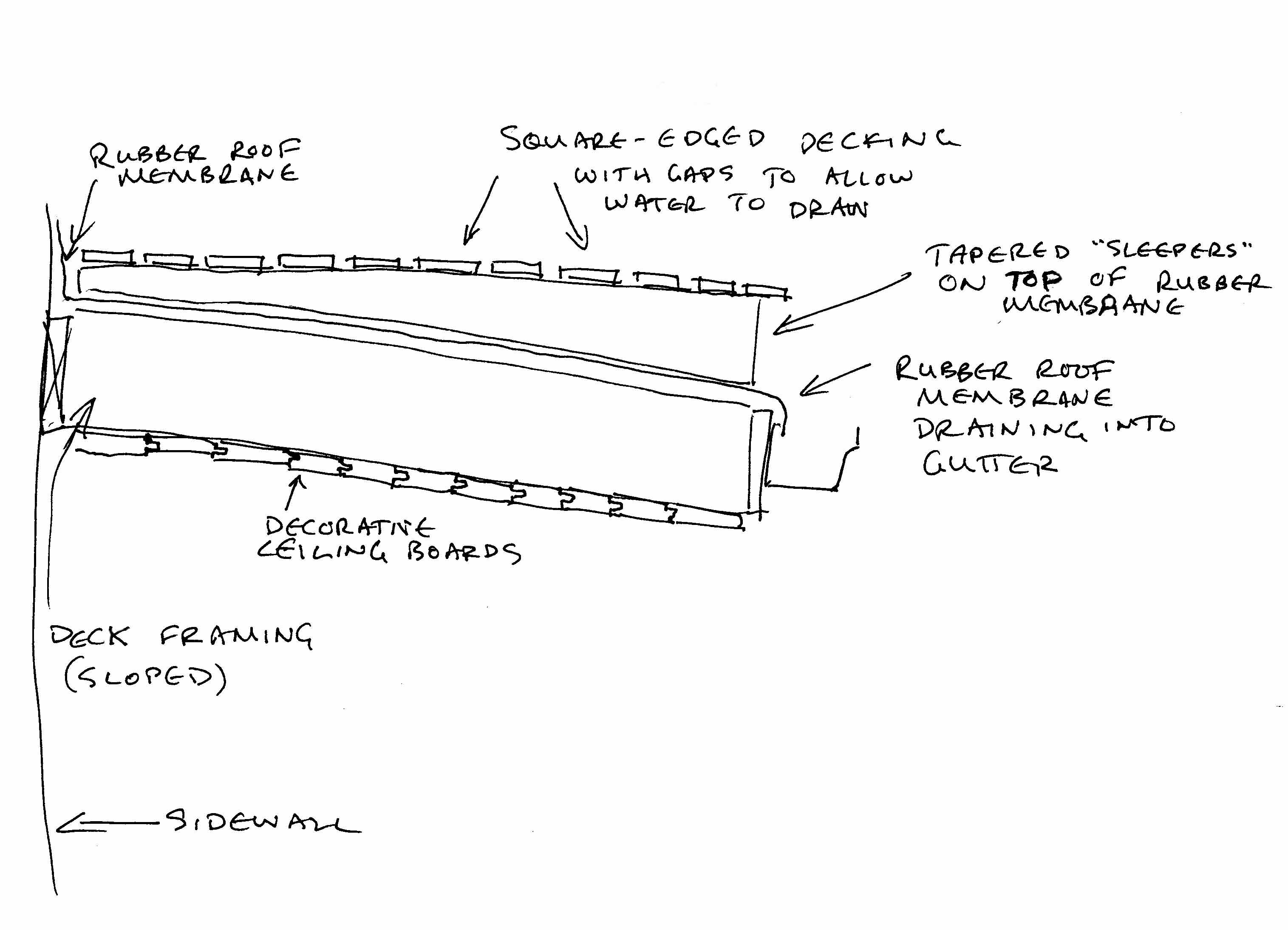
In this arrangement, the deck framing is sloped away from the house, and there is a rubber roofing membrane covering the deck surface and dumping into a gutter. A walkable decking material is installed over sleepers (framing members which sit on top of a lower surface) which rest on the rubber. The sleepers can be tapered so that the uppermost deck surface can be level. Square-edged decking boards, installed with gaps between each board, allow water to drain to the rubber roofing membrane. In this installation, decorative boards can be installed on the bottom of the deck joists to provide a finished ceiling below.
A simpler design would also work:
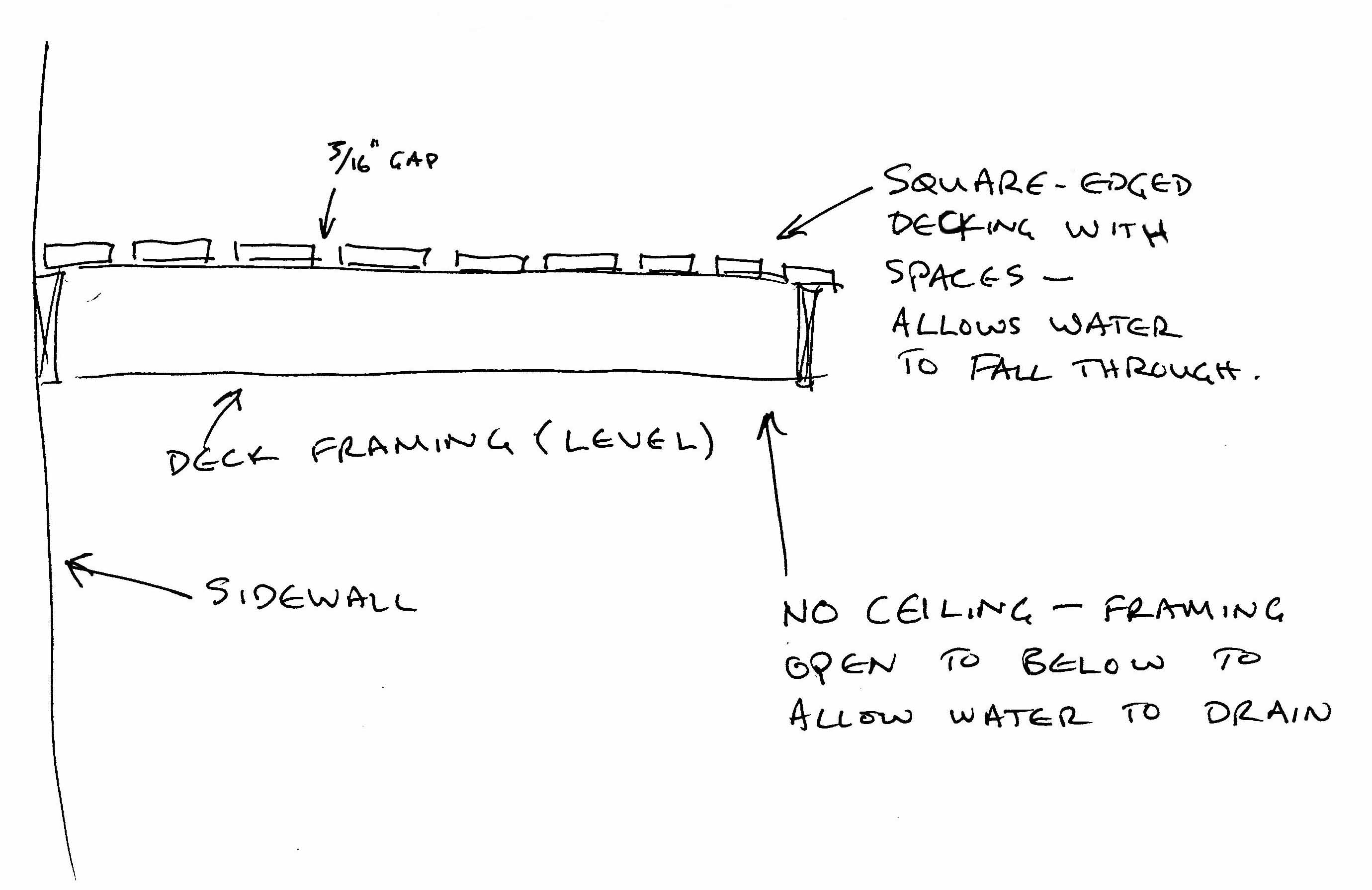
In this case, there is no sloped framing and no waterproof roofing membrane. Instead, square-edged decking is installed with gaps between the boards (we like 3/16″ — not so large as to kill wearers of high heels and not so small that leaves would clog the gaps). Water drains straight through the deck to the surface below, so no finished ceiling is possible, and the deck doesn’t afford any weather protection to the level below. But there is no opportunity for water to collect and cause mischief.
In the case of the JP decks, mischief happened. The t&g flooring and the plywood underneath it trapped water, and because the fir decking is not naturally rot-resistant, it started to fail 5 or 6 years after it was installed. The generally wet conditions also promoted rot in the pine trim boards.
Pine riser, seen from below:

Skirt trim at base of deck:
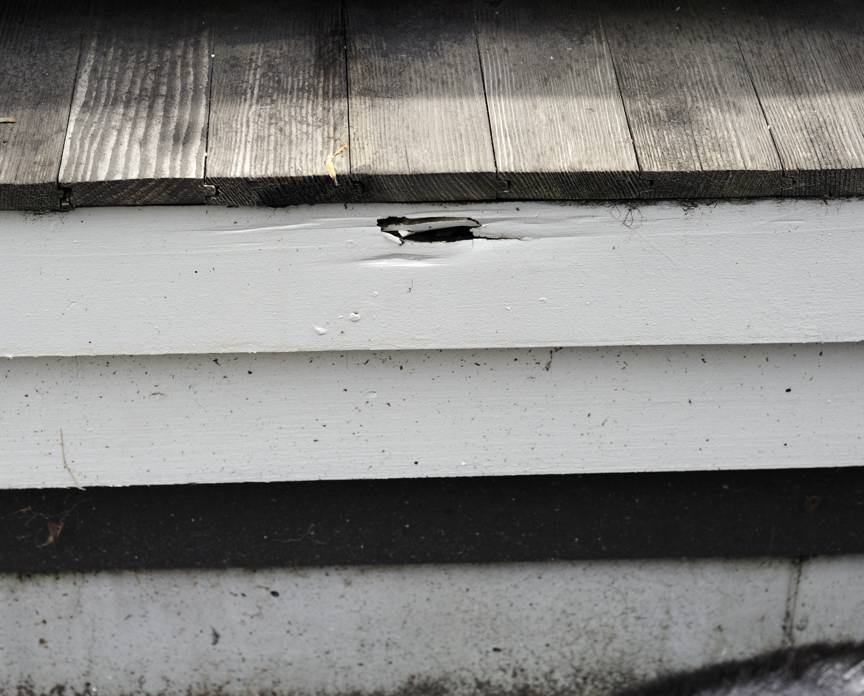
Our next step was to investigate whether the chronically wet conditions had compromised the structure of the decks. We removed the plastic “beadboard” on the ceilings at the first and second floors to reveal the deck framing. The good news was that the floor joists were made from pressure-treated lumber, and that they were still in good condition. However, the joist hangers and lag bolts in the ledger were significantly corroded.
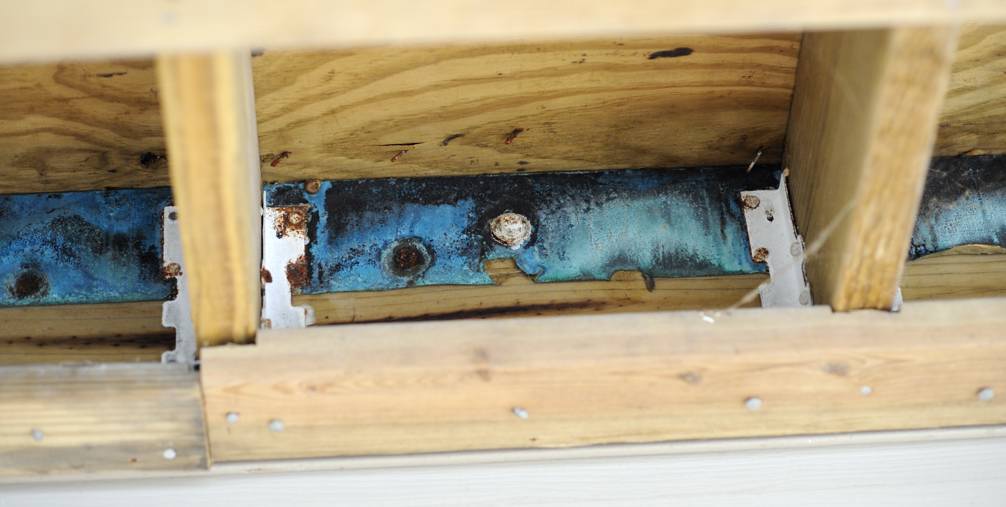
The moisture inside the deck floor system likely contributed to the corrosion, but another factor was likely more important.
For many years, the preservative used to treat outdoor wood was chromated copper arsenate (CCA). Concerns over potential toxicity of any arsenic that might leach out of the wood, though, led to the phase-out of CCA. Starting in January 2004, the US EPA mandated that pressure-treated wood used in residential settings be free of arsenic. In New England, the predominant replacement for CCA has been ammoniacal copper quaternary salt (ACQ), a combined fungicide and insecticide.
But the law of unintended consequences is a harsh mistress. While ACQ is an effective wood preservative, it turns out to be dramatically more corrosive that the preservative it replaced. ACQ contains much more copper than CCA, and the copper is more readily soluble in water, setting up perfect conditions for galvanic corrosion to set in. Aluminum and steel are particularly vulnerable, with zinc somewhat less so. The upshot was that builders soon observed their nails, screws, and hangers turning into powder when in contact with the new pressure-treated wood. The photo below shows a particularly dramatic example of galvanic corrosion from the same deck. Steel nails installed through copper flashing have completely disintegrated, along with sections of the flashing.
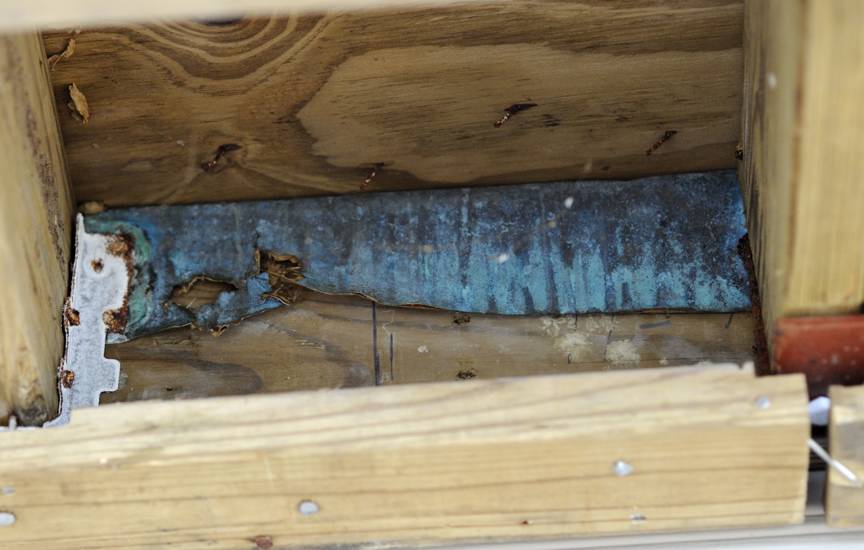
It seems that the company that produces ACQ was aware of the corrosion problem, but the information was slow to reach many carpenters. (Framing lumber, after all, rarely comes with an instruction manual.) The corrosion potential can be successfully managed with triply-galvanized joist hangers, epoxy-coated screws, and stainless steel bolts, all standard practice in 2012.
The deck in question, though, was built in 2005. When I examined the joist hangers, I could see that they were not the extra-galvanized variety now in common use (Simpson Zmax). The high moisture levels resulting from the faulty construction, combined with the extra copper in the ACQ, overwhelmed the thin layer of zinc on the hangers. We consulted with a structural engineer who indicated that all of the hangers, along with all of the lag bolts in the ledger, would need to be replaced immediately.
There was one bright spot in our investigations of this deck: It seems that the builders were careful in flashing behind the deck ledgers, and the sidewall of the main structure looks like it has remained dry.
We are now working with the owners of the building to determine the best way to modify the decks to ensure their safety and longevity. Stay tuned.
Tagged: ACQ, CCA, deck building, galvanic corrosion, Musti, pressure-treated lumber